Understanding the Key Components and Fixing Techniques for Product Packaging Equipment Upkeep
Efficient maintenance of packaging machines depends upon a detailed understanding of their vital elements, including the framework, drive system, and sealing systems. Identifying usual maintenance concerns, paired with the implementation of preventative techniques and fixing methods, can considerably boost equipment reliability. The choice of repair service practices, including the use of OEM parts and the significance of licensed technicians, plays a critical role in decreasing downtime. To really understand the intricacies of these systems and their maintenance, one must think about the more comprehensive implications of ignoring these vital practices.
Secret Components of Packaging Machines
Packaging makers consist of a number of key elements that interact to make certain efficient and efficient product packaging procedures. At the core of these makers is the framework, which provides architectural integrity and houses the various operating components. The drive system, frequently a combination of gears and electric motors, helps with the movement of elements, allowing accurate procedure throughout the packaging cycle.
An additional vital part is the conveyor system, which transfers items with different phases of the packaging procedure. This is often complemented by sensing units and controls that check the position and rate of things, making certain synchronization and reducing errors. The filling system is critical for precisely dispensing the best amount of product right into packages, whether in liquid, powder, or solid form.
Sealing systems, including warm sealers or adhesive applicators, play a vital function in safeguarding packages, preventing contamination and prolonging service life. Additionally, labeling systems are indispensable for giving necessary product info, making sure compliance with laws. Lastly, the control panel, furnished with user-friendly user interfaces, enables drivers to handle device functions, monitor performance, and make modifications as required, ensuring optimum productivity and performance in packaging operations.
Typical Maintenance Problems
Reliable procedure of product packaging makers depends greatly on regular upkeep to avoid typical issues that can interrupt manufacturing. Among these issues, mechanical damage prevails, particularly in components like seals, conveyors, and motors, which can cause unanticipated downtimes. Furthermore, misalignment of parts can lead to ineffective procedure, causing products to be inaccurately packaged or damaged throughout the process.
One more typical upkeep concern entails the buildup of dust and particles, which can hinder the device's sensors and moving parts. packaging machine repair service. This not just impacts efficiency yet can additionally position safety risks. Lubrication failings can lead to enhanced rubbing, resulting in getting too hot and eventual element failing.
Electric issues, usually stemming from loosened links or damaged electrical wiring, can interrupt equipment features, causing considerable production delays. Software application problems due to improper setups or out-of-date programs can hinder the device's operation, demanding instant treatment. Resolving these typical upkeep problems proactively is crucial for ensuring optimal efficiency and long review life of packaging equipment.
Preventative Maintenance Approaches
Carrying out preventative upkeep strategies is important for maintaining the efficiency and reliability of packaging machines. These strategies encompass a systematic method to maintenance, concentrating on the regular inspection and servicing of tools to preempt potential failures. By adhering to a set up upkeep program, drivers can determine wear and tear on elements prior to they result in significant break downs.
Crucial element of a preventative maintenance approach include regular inspections, cleaning, lubrication, and element substitutes based on supplier suggestions. Using lists can simplify this process, making certain that no necessary jobs are ignored. In addition, preserving precise records of upkeep tasks help in tracking the maker's efficiency with time, assisting in notified decision-making pertaining to future maintenance needs.
Training staff on the value of preventative upkeep boosts compliance and promotes a culture of positive care. Executing an anticipating maintenance component, using information analytics and sensing unit innovation, can even more enhance machinery performance by forecasting failings prior to they occur.
Repairing Methods
When confronted with breakdowns or inefficiencies in packaging equipments, using methodical troubleshooting techniques is necessary for recognizing and settling problems swiftly. The very first step in efficient troubleshooting is to establish a clear understanding of the device's operational specifications and efficiency metrics. This involves reviewing the equipment's specs, in addition to any kind of mistake codes or signals displayed.
Following, drivers ought to carry out her explanation an aesthetic evaluation, examining for obvious signs of misalignment, damage, or wear. This often includes analyzing belts, sensing units, and gears to identify potential root causes of breakdown. Gathering functional data, such as production prices and downtime logs, can also supply understandings right into persisting issues.
As soon as possible issues are recognized, making use of a logical approach to isolate the origin is crucial. This might require testing specific elements or systems in a controlled manner. Involving in conversations with drivers that engage with the equipment frequently can produce important comments concerning unusual habits or patterns.
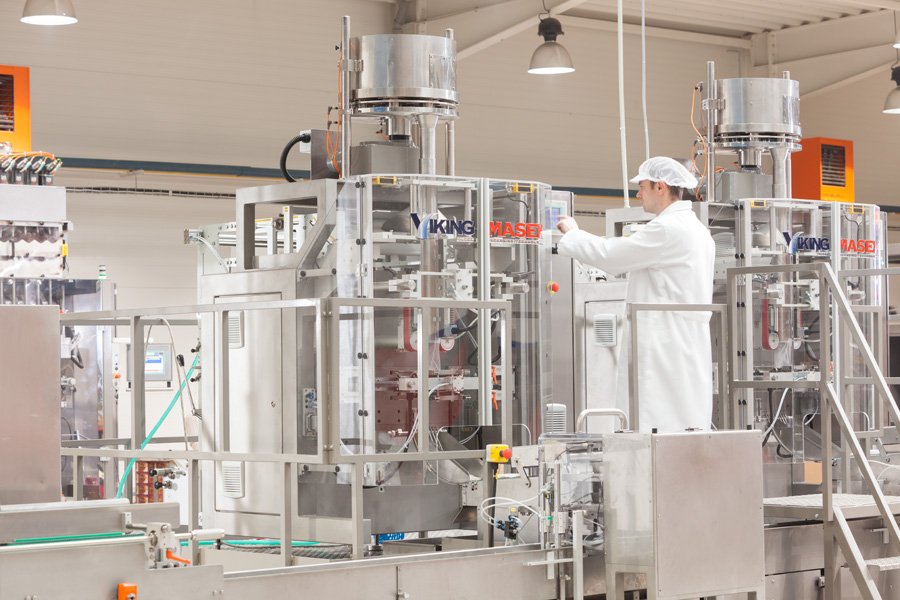
Repair Work and Replacement Best Practices
An extensive understanding of repair and substitute best techniques is vital for maintaining the durability and effectiveness of packaging machines. Consistently analyzing the condition of equipment components permits timely treatment, protecting against more significant issues that can result in expensive downtimes.
When repair work are essential, it is necessary to utilize OEM (Original Devices Supplier) parts to ensure compatibility and efficiency. This not only maintains the integrity of the machine but also upholds guarantee agreements. In addition, it is advisable to keep an inventory of vital extra parts to help with quick replacements and reduce functional disturbances.
For intricate repair work, involving certified professionals with specialized training in product packaging equipment is recommended. They possess the experience to diagnose issues properly and implement repair work successfully. Recording all repair activities and parts replacements is vital for keeping a thorough maintenance history, which can aid in future troubleshooting.
Lastly, executing a positive approach, consisting of regular evaluations and anticipating upkeep strategies, enhances the reliability of product packaging devices. By adhering to these finest techniques, businesses can make sure optimum maker efficiency, reduce functional risks, and expand tools life-span.
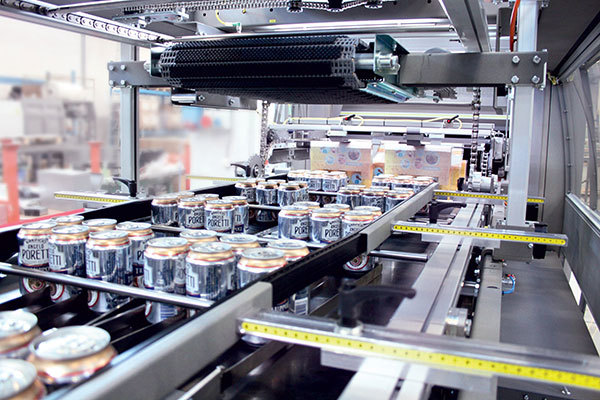
Verdict
In final thought, an extensive understanding of product packaging device elements and reliable maintenance techniques is essential for optimal performance. By carrying out these practices, organizations can make certain the long life and effectiveness of packaging machines, inevitably adding to boosted functional performance and lowered costs (packaging machine repair service).
Effective upkeep of packaging makers pivots on a comprehensive understanding of their essential components, consisting site here of the frame, drive system, and sealing systems.Efficient procedure of packaging makers relies heavily on normal upkeep to avoid usual problems that can interrupt production.Applying preventative maintenance techniques is essential for maintaining the effectiveness and integrity of packaging equipments. Furthermore, keeping exact records of maintenance activities help in tracking the equipment's efficiency over time, assisting in notified decision-making concerning future maintenance demands.

Comments on “Packaging Machine Repair Service: Prevent Costly Breakdowns with Specialist Aid”